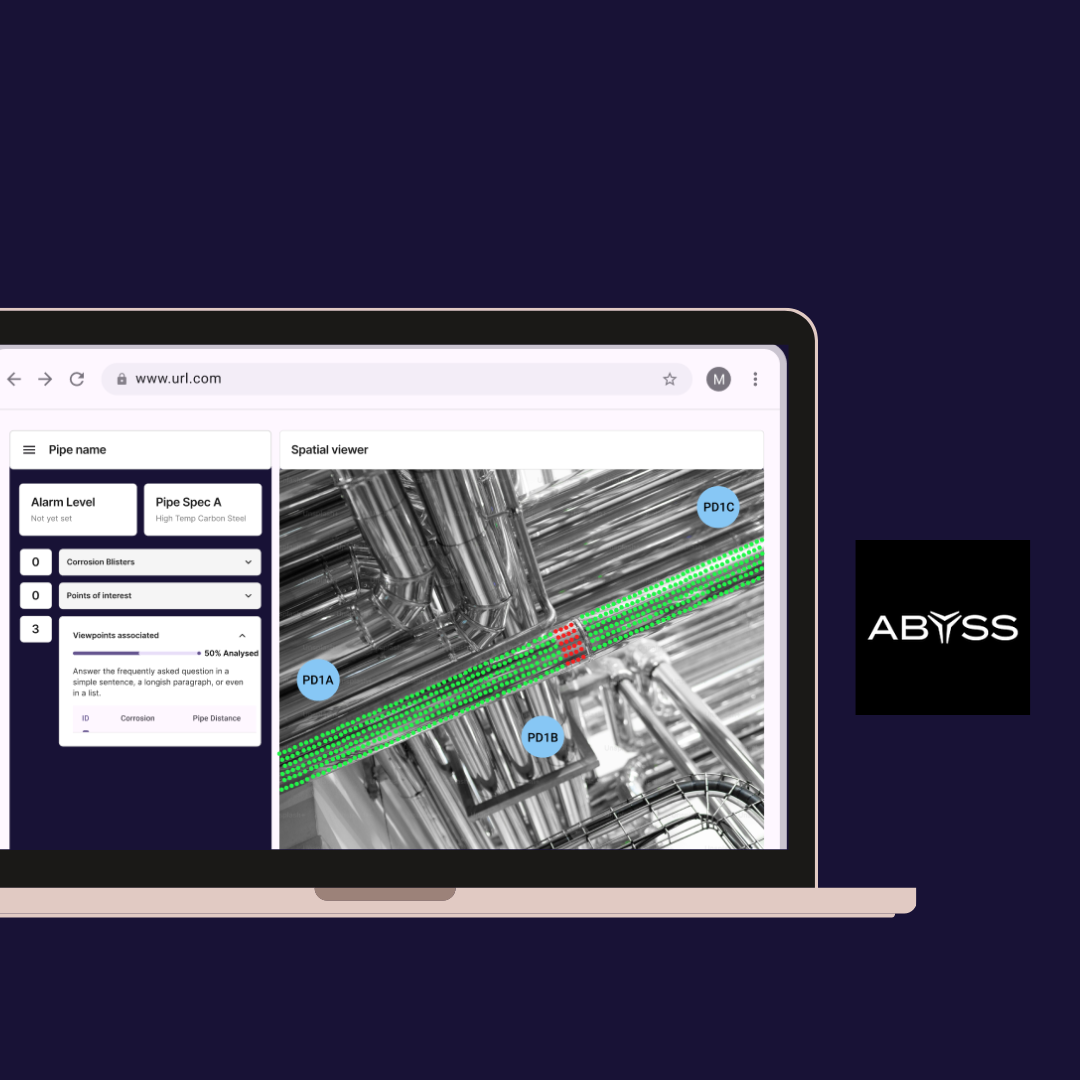
Project Summary
- Client: Abyss Solutions
- Role: UX Designer
- Duration: May 2022 – May 2023
- Focus: Client research, navigation UX, inspection workflow support
In this second engagement with Abyss, I was tasked with understanding how external clients—specifically mechanical integrity (MI) engineers and field inspectors—use Abyss Fabric during oil platform inspection planning. These inspections (known as “walk-downs”) are physically intensive and require high spatial awareness. My work aimed to uncover pain points in the existing interface, assess the value clients derive from Fabric, and propose ways to improve planning efficiency through smarter tool integration.
While the project was eventually deprioritized due to a management pivot, I uncovered valuable design insights about spatial navigation, planning inefficiencies, and domain-specific constraints that will inform future versions of the product.
Team & Stakeholders
Worked with the Product Manager, Product Owner, Team Lead, ML Lead, 4 Developers, and a Customer Success Engineer Conducted interviews and usability testing with 5 internal users and feedback from client-facing engineers
Challenge
Clients described Abyss Fabric as “clunky”—but without clear context. My challenge was to unpack this feedback, understand where the breakdowns occurred, and evaluate how MI engineers interact with the platform while preparing their inspection campaigns. In particular, the product team wanted to know if we could integrate spatial data from isometric (2D) oil platform drawings directly into Fabric to assist planning.
UX Process & Solutions
Discovery
- Conducted contextual inquiries and workflow mapping with MI engineers and field inspectors
- Shadowed internal usage sessions to understand shared friction points between internal and client-facing users
- Focused specifically on inspection preparation workflows and spatial comprehension
Key Insights
- Navigation issues—what clients described as “clunky” stemmed from inconsistent spatial orientation and limited visibility of inspection targets
- Planning value—Fabric was under-leveraged during early campaign planning; engineers often resorted to offline tools
- Isometric plan pain—Reading 2D drawings for 3D environments was inefficient and error-prone, especially under time pressure
- Regulatory nuance—External corrosion findings could only guide prioritization, not serve as definitive proof due to compliance constraints
Design Opportunities
- Explore overlays of location data and inspection target mapping within Fabric’s 3D view
- Prototype a planning interface for inspection equipment and access logistics
- Align navigation patterns with internal tooling to reduce friction across roles
Outcomes
Although the project was paused due to a change in company direction, the research provided:
- Validation that clients do find value in Fabric—particularly in visualizing inspection findings
- Clarity on the friction behind “clunkiness,” shared by both internal and external users
- New design pathways for integrating isometric plan data into a spatial interface
- Strategic framing for turning Fabric into a planning as well as reporting tool
Next Steps
This project informed the groundwork for my third initiative: a conceptual tool for marine terminal risk assessments, helping oil companies perform faster, more comprehensive evaluations with cost-benefit framing. The idea was to give clients control over prioritizing inspection zones at terminals in the same way we were working toward for offshore platforms.
Learnings
This project expanded my ability to support dual-sided platforms, those used by both internal experts and external engineers with different regulatory and contextual needs. It also refined my approach to dealing with ambiguous feedback like “clunky,” encouraging deeper investigation into usability language and system perception.